What are the Product Standards for Standard Capacitors?
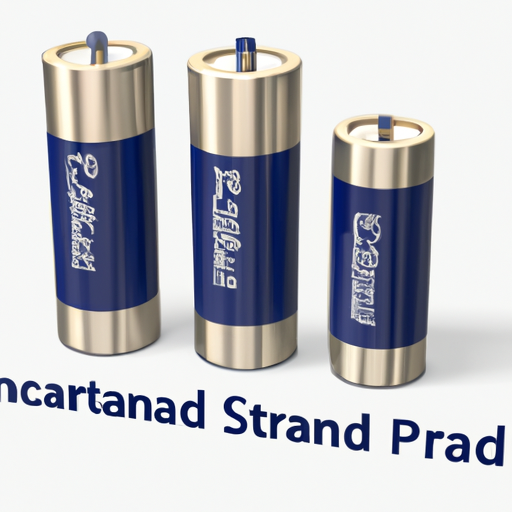
I. Introduction
Capacitors are fundamental components in electronic circuits, serving various functions such as energy storage, filtering, and timing. Standard capacitors, in particular, are precision components used as references in testing and calibration. The importance of product standards in the electronics industry cannot be overstated; they ensure quality, reliability, and safety across a wide range of applications. This blog post aims to explore the product standards for standard capacitors, detailing their significance, the organizations involved in standardization, and the challenges and future trends in this field.
II. Understanding Capacitors
A. Basic Principles of Capacitors
Capacitors are passive electronic components that store electrical energy in an electric field. They consist of two conductive plates separated by an insulating material known as a dielectric. When a voltage is applied across the plates, an electric field develops, allowing the capacitor to store energy. The primary function of capacitors is to store and release energy, making them essential in various electronic applications.
There are several types of capacitors, including ceramic, electrolytic, tantalum, and film capacitors, each with unique characteristics and applications. For instance, ceramic capacitors are often used in high-frequency applications due to their low equivalent series resistance (ESR), while electrolytic capacitors are favored for their high capacitance values in power supply circuits.
B. Applications of Capacitors in Electronic Circuits
Capacitors play a crucial role in electronic circuits, serving multiple purposes:
1. **Energy Storage**: Capacitors store energy for later use, providing power during brief interruptions in supply.
2. **Filtering and Smoothing**: In power supply circuits, capacitors filter out voltage fluctuations, smoothing the output to provide a stable voltage.
3. **Timing Applications**: Capacitors are used in timing circuits, where they charge and discharge at specific rates to create time delays.
III. The Need for Product Standards
The need for product standards in the capacitor industry arises from several factors:
A. Ensuring Quality and Reliability
Product standards help ensure that capacitors meet specific performance criteria, which is vital for the reliability of electronic devices. High-quality capacitors reduce the risk of failure, which can lead to costly repairs and safety hazards.
B. Facilitating Interoperability Between Components
Standardization allows different manufacturers to produce components that can work together seamlessly. This interoperability is crucial in complex electronic systems where various components must function in harmony.
C. Compliance with Safety Regulations
Product standards often include safety regulations that manufacturers must adhere to, ensuring that capacitors do not pose risks to users or the environment. Compliance with these standards is essential for market acceptance and consumer trust.
D. Enhancing Consumer Confidence
When consumers know that a product meets established standards, they are more likely to trust its quality and performance. This confidence is crucial in a competitive market where consumers have many options.
IV. Key Organizations Involved in Standardization
Several organizations play a pivotal role in the standardization of capacitors:
A. International Electrotechnical Commission (IEC)
The IEC is a global organization that develops and publishes international standards for electrical and electronic technologies. The IEC 60384 series specifically addresses capacitors, providing guidelines for fixed capacitors, including performance, testing, and safety requirements.
B. Institute of Electrical and Electronics Engineers (IEEE)
The IEEE is a leading organization in the development of standards for electrical and electronic systems. It contributes to capacitor standards by providing guidelines that ensure compatibility and performance in various applications.
C. American National Standards Institute (ANSI)
ANSI oversees the development of voluntary consensus standards for products, services, and systems in the United States. It plays a crucial role in establishing standards relevant to capacitors, ensuring they meet national and international requirements.
D. Other Relevant Organizations
Organizations such as JEDEC (Joint Electron Device Engineering Council) and EIA (Electronic Industries Alliance) also contribute to the standardization of capacitors, focusing on specific applications and technologies.
V. Major Product Standards for Standard Capacitors
A. IEC 60384 Series
The IEC 60384 series is a comprehensive set of standards that covers fixed capacitors for use in electronic equipment. It includes various specifications, such as:
IEC 60384-14: This standard focuses on fixed capacitors for use in electronic equipment, detailing performance requirements, testing methods, and safety considerations.
B. MIL-PRF-39014
MIL-PRF-39014 is a military specification that outlines the requirements for capacitors used in military and aerospace applications. These standards ensure that capacitors can withstand extreme conditions, making them suitable for critical applications where reliability is paramount.
C. ISO 9001
ISO 9001 is a quality management standard that applies to organizations across various industries, including capacitor manufacturing. Compliance with ISO 9001 ensures that manufacturers maintain consistent quality in their products and processes.
D. RoHS and REACH Compliance
RoHS (Restriction of Hazardous Substances) and REACH (Registration, Evaluation, Authorisation, and Restriction of Chemicals) are environmental standards that affect capacitor production. These regulations limit the use of hazardous materials in electronic components, promoting sustainability and safety in manufacturing.
VI. Testing and Certification Processes
A. Overview of Testing Methods for Capacitors
Testing is a critical aspect of ensuring that capacitors meet established standards. Common testing methods include:
1. **Electrical Testing**: This includes measuring capacitance, ESR, and voltage rating to ensure that capacitors perform as expected.
2. **Environmental Testing**: Capacitors are subjected to various environmental conditions, such as temperature and humidity, to assess their reliability and performance under different scenarios.
B. Certification Processes for Compliance with Standards
Certification processes involve third-party testing laboratories that evaluate capacitors against established standards. These laboratories provide certification marks, such as UL (Underwriters Laboratories) and CE (Conformité Européenne), indicating compliance with safety and performance standards.
VII. Challenges in Standardization
Despite the importance of standardization, several challenges persist:
A. Rapid Technological Advancements
The fast pace of technological innovation can outstrip existing standards, making it difficult for organizations to keep up. New capacitor technologies may require the development of new standards to ensure safety and performance.
B. Variability in Manufacturing Processes
Differences in manufacturing processes can lead to variability in capacitor performance, complicating standardization efforts. Ensuring consistent quality across different manufacturers is a significant challenge.
C. Globalization and Differing Regional Standards
As the electronics industry becomes increasingly globalized, manufacturers must navigate differing regional standards. This complexity can hinder the adoption of universal standards and create barriers to market entry.
D. Balancing Innovation with Compliance
Manufacturers must balance the need for innovation with compliance to existing standards. Striking this balance is crucial for fostering technological advancements while ensuring safety and reliability.
VIII. Future Trends in Capacitor Standards
A. Emerging Technologies and Their Impact on Standards
As new technologies, such as electric vehicles and renewable energy systems, gain traction, capacitor standards will need to evolve to address the unique requirements of these applications.
B. The Role of Sustainability in Future Standards
Sustainability is becoming a critical consideration in product standards. Future capacitor standards may place greater emphasis on environmentally friendly materials and manufacturing processes.
C. Anticipated Changes in Regulatory Frameworks
Regulatory frameworks are likely to evolve in response to emerging technologies and environmental concerns. Manufacturers must stay informed about these changes to ensure compliance and maintain market access.
IX. Conclusion
In conclusion, product standards for standard capacitors are essential for ensuring quality, reliability, and safety in the electronics industry. As technology continues to advance, the need for collaboration among stakeholders, including manufacturers, standardization organizations, and regulatory bodies, will be crucial. By working together, these entities can develop and maintain standards that not only meet current needs but also anticipate future challenges and opportunities in the capacitor market.
X. References
1. International Electrotechnical Commission (IEC). (n.d.). IEC 60384 Series.
2. Institute of Electrical and Electronics Engineers (IEEE). (n.d.). IEEE Standards.
3. American National Standards Institute (ANSI). (n.d.). ANSI Standards.
4. MIL-PRF-39014. (n.d.). Military Specification for Capacitors.
5. ISO 9001. (n.d.). Quality Management Systems.
6. RoHS and REACH Compliance. (n.d.). Environmental Standards.
This blog post provides a comprehensive overview of the product standards for standard capacitors, highlighting their significance, the organizations involved, and the challenges and future trends in the field. By understanding these standards, manufacturers and consumers can ensure the reliability and safety of electronic components in an ever-evolving industry.
What are the Product Standards for Standard Capacitors?
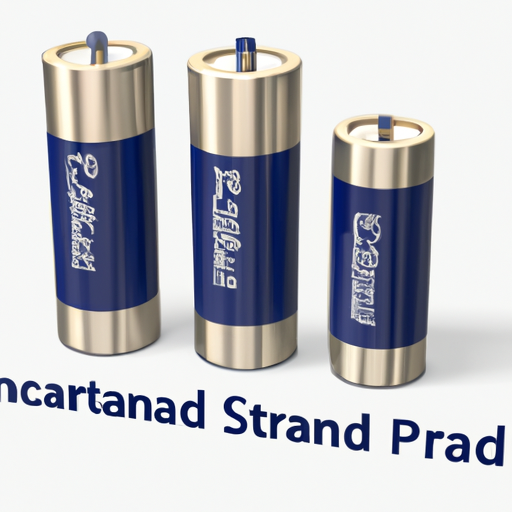
I. Introduction
Capacitors are fundamental components in electronic circuits, serving various functions such as energy storage, filtering, and timing. Standard capacitors, in particular, are precision components used as references in testing and calibration. The importance of product standards in the electronics industry cannot be overstated; they ensure quality, reliability, and safety across a wide range of applications. This blog post aims to explore the product standards for standard capacitors, detailing their significance, the organizations involved in standardization, and the challenges and future trends in this field.
II. Understanding Capacitors
A. Basic Principles of Capacitors
Capacitors are passive electronic components that store electrical energy in an electric field. They consist of two conductive plates separated by an insulating material known as a dielectric. When a voltage is applied across the plates, an electric field develops, allowing the capacitor to store energy. The primary function of capacitors is to store and release energy, making them essential in various electronic applications.
There are several types of capacitors, including ceramic, electrolytic, tantalum, and film capacitors, each with unique characteristics and applications. For instance, ceramic capacitors are often used in high-frequency applications due to their low equivalent series resistance (ESR), while electrolytic capacitors are favored for their high capacitance values in power supply circuits.
B. Applications of Capacitors in Electronic Circuits
Capacitors play a crucial role in electronic circuits, serving multiple purposes:
1. **Energy Storage**: Capacitors store energy for later use, providing power during brief interruptions in supply.
2. **Filtering and Smoothing**: In power supply circuits, capacitors filter out voltage fluctuations, smoothing the output to provide a stable voltage.
3. **Timing Applications**: Capacitors are used in timing circuits, where they charge and discharge at specific rates to create time delays.
III. The Need for Product Standards
The need for product standards in the capacitor industry arises from several factors:
A. Ensuring Quality and Reliability
Product standards help ensure that capacitors meet specific performance criteria, which is vital for the reliability of electronic devices. High-quality capacitors reduce the risk of failure, which can lead to costly repairs and safety hazards.
B. Facilitating Interoperability Between Components
Standardization allows different manufacturers to produce components that can work together seamlessly. This interoperability is crucial in complex electronic systems where various components must function in harmony.
C. Compliance with Safety Regulations
Product standards often include safety regulations that manufacturers must adhere to, ensuring that capacitors do not pose risks to users or the environment. Compliance with these standards is essential for market acceptance and consumer trust.
D. Enhancing Consumer Confidence
When consumers know that a product meets established standards, they are more likely to trust its quality and performance. This confidence is crucial in a competitive market where consumers have many options.
IV. Key Organizations Involved in Standardization
Several organizations play a pivotal role in the standardization of capacitors:
A. International Electrotechnical Commission (IEC)
The IEC is a global organization that develops and publishes international standards for electrical and electronic technologies. The IEC 60384 series specifically addresses capacitors, providing guidelines for fixed capacitors, including performance, testing, and safety requirements.
B. Institute of Electrical and Electronics Engineers (IEEE)
The IEEE is a leading organization in the development of standards for electrical and electronic systems. It contributes to capacitor standards by providing guidelines that ensure compatibility and performance in various applications.
C. American National Standards Institute (ANSI)
ANSI oversees the development of voluntary consensus standards for products, services, and systems in the United States. It plays a crucial role in establishing standards relevant to capacitors, ensuring they meet national and international requirements.
D. Other Relevant Organizations
Organizations such as JEDEC (Joint Electron Device Engineering Council) and EIA (Electronic Industries Alliance) also contribute to the standardization of capacitors, focusing on specific applications and technologies.
V. Major Product Standards for Standard Capacitors
A. IEC 60384 Series
The IEC 60384 series is a comprehensive set of standards that covers fixed capacitors for use in electronic equipment. It includes various specifications, such as:
IEC 60384-14: This standard focuses on fixed capacitors for use in electronic equipment, detailing performance requirements, testing methods, and safety considerations.
B. MIL-PRF-39014
MIL-PRF-39014 is a military specification that outlines the requirements for capacitors used in military and aerospace applications. These standards ensure that capacitors can withstand extreme conditions, making them suitable for critical applications where reliability is paramount.
C. ISO 9001
ISO 9001 is a quality management standard that applies to organizations across various industries, including capacitor manufacturing. Compliance with ISO 9001 ensures that manufacturers maintain consistent quality in their products and processes.
D. RoHS and REACH Compliance
RoHS (Restriction of Hazardous Substances) and REACH (Registration, Evaluation, Authorisation, and Restriction of Chemicals) are environmental standards that affect capacitor production. These regulations limit the use of hazardous materials in electronic components, promoting sustainability and safety in manufacturing.
VI. Testing and Certification Processes
A. Overview of Testing Methods for Capacitors
Testing is a critical aspect of ensuring that capacitors meet established standards. Common testing methods include:
1. **Electrical Testing**: This includes measuring capacitance, ESR, and voltage rating to ensure that capacitors perform as expected.
2. **Environmental Testing**: Capacitors are subjected to various environmental conditions, such as temperature and humidity, to assess their reliability and performance under different scenarios.
B. Certification Processes for Compliance with Standards
Certification processes involve third-party testing laboratories that evaluate capacitors against established standards. These laboratories provide certification marks, such as UL (Underwriters Laboratories) and CE (Conformité Européenne), indicating compliance with safety and performance standards.
VII. Challenges in Standardization
Despite the importance of standardization, several challenges persist:
A. Rapid Technological Advancements
The fast pace of technological innovation can outstrip existing standards, making it difficult for organizations to keep up. New capacitor technologies may require the development of new standards to ensure safety and performance.
B. Variability in Manufacturing Processes
Differences in manufacturing processes can lead to variability in capacitor performance, complicating standardization efforts. Ensuring consistent quality across different manufacturers is a significant challenge.
C. Globalization and Differing Regional Standards
As the electronics industry becomes increasingly globalized, manufacturers must navigate differing regional standards. This complexity can hinder the adoption of universal standards and create barriers to market entry.
D. Balancing Innovation with Compliance
Manufacturers must balance the need for innovation with compliance to existing standards. Striking this balance is crucial for fostering technological advancements while ensuring safety and reliability.
VIII. Future Trends in Capacitor Standards
A. Emerging Technologies and Their Impact on Standards
As new technologies, such as electric vehicles and renewable energy systems, gain traction, capacitor standards will need to evolve to address the unique requirements of these applications.
B. The Role of Sustainability in Future Standards
Sustainability is becoming a critical consideration in product standards. Future capacitor standards may place greater emphasis on environmentally friendly materials and manufacturing processes.
C. Anticipated Changes in Regulatory Frameworks
Regulatory frameworks are likely to evolve in response to emerging technologies and environmental concerns. Manufacturers must stay informed about these changes to ensure compliance and maintain market access.
IX. Conclusion
In conclusion, product standards for standard capacitors are essential for ensuring quality, reliability, and safety in the electronics industry. As technology continues to advance, the need for collaboration among stakeholders, including manufacturers, standardization organizations, and regulatory bodies, will be crucial. By working together, these entities can develop and maintain standards that not only meet current needs but also anticipate future challenges and opportunities in the capacitor market.
X. References
1. International Electrotechnical Commission (IEC). (n.d.). IEC 60384 Series.
2. Institute of Electrical and Electronics Engineers (IEEE). (n.d.). IEEE Standards.
3. American National Standards Institute (ANSI). (n.d.). ANSI Standards.
4. MIL-PRF-39014. (n.d.). Military Specification for Capacitors.
5. ISO 9001. (n.d.). Quality Management Systems.
6. RoHS and REACH Compliance. (n.d.). Environmental Standards.
This blog post provides a comprehensive overview of the product standards for standard capacitors, highlighting their significance, the organizations involved, and the challenges and future trends in the field. By understanding these standards, manufacturers and consumers can ensure the reliability and safety of electronic components in an ever-evolving industry.