Manufacturing Processes of the Latest Neutral Point Resistors
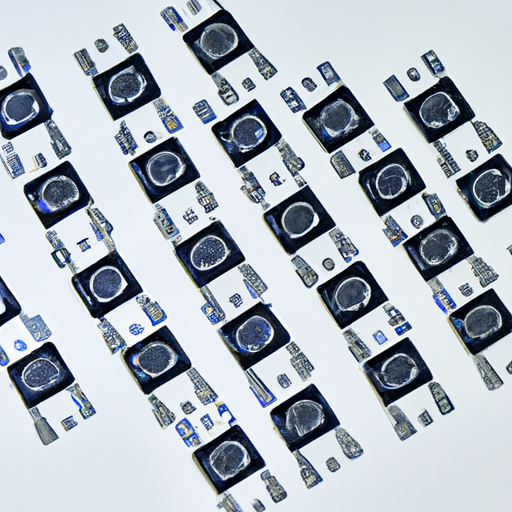
I. Introduction
Neutral Point Resistors (NPRs) are critical components in modern electrical systems, particularly in applications involving power electronics and renewable energy. These resistors play a vital role in managing voltage levels and ensuring the stability of electrical systems. As the demand for efficient and reliable electrical solutions grows, understanding the manufacturing processes of the latest NPRs becomes increasingly important. This blog post will explore the various stages involved in the production of NPRs, from raw material selection to innovative manufacturing techniques.
II. Understanding Neutral Point Resistors
A. Function and Application of NPRs
NPRs serve a crucial function in electrical systems by providing a path for fault currents to flow, thereby protecting sensitive equipment from damage. They are commonly used in power electronics, such as inverters and converters, where they help maintain voltage balance and prevent overvoltage conditions. Additionally, NPRs are integral to renewable energy systems, including wind and solar power installations, where they ensure the safe operation of electrical grids.
B. Types of Neutral Point Resistors
NPRs can be categorized into two main types: fixed resistors and variable resistors. Fixed NPRs have a predetermined resistance value, making them suitable for applications where consistent performance is required. In contrast, variable NPRs allow for adjustable resistance, providing flexibility in applications where conditions may change.
C. Key Specifications and Performance Metrics
When evaluating NPRs, several key specifications and performance metrics must be considered, including resistance value, power rating, thermal stability, and response time. These factors determine how effectively an NPR can perform its intended function in various electrical systems.
III. Raw Materials for NPR Manufacturing
A. Types of Materials Used
The manufacturing of NPRs involves a variety of raw materials. Conductive materials, such as carbon and metal alloys, are essential for creating the resistive elements. These materials must possess specific electrical properties to ensure optimal performance. Insulating materials, including ceramics and polymers, are also crucial for preventing electrical leakage and ensuring safety.
B. Quality Control of Raw Materials
Quality control is a vital aspect of the manufacturing process. Raw materials must be thoroughly tested to ensure they meet the required specifications. This includes assessing their electrical conductivity, thermal properties, and mechanical strength. Ensuring high-quality materials is essential for the reliability and longevity of the final product.
C. Environmental Considerations in Material Selection
In recent years, there has been a growing emphasis on sustainability in manufacturing. Manufacturers are increasingly selecting eco-friendly materials and processes to minimize their environmental impact. This includes using recyclable materials and reducing waste during production.
IV. Manufacturing Processes
A. Design and Prototyping
The manufacturing process begins with design and prototyping. Computer-aided design (CAD) tools are employed to create detailed models of NPRs. These models allow engineers to simulate and test various designs before moving to production. This stage is crucial for identifying potential issues and optimizing the design for performance and manufacturability.
B. Fabrication Techniques
Once the design is finalized, fabrication techniques come into play. This involves cutting and shaping the raw materials to create the various components of the NPR. Advanced machining techniques, such as laser cutting and CNC machining, are often used to achieve precise dimensions and tolerances.
C. Resistance Element Production
The production of the resistive elements is a critical step in the manufacturing process. Various methods are employed to create these elements, including sintering, where powdered materials are heated to form a solid mass. Techniques for achieving desired resistance values may involve adjusting the composition of the materials or altering the dimensions of the resistive elements.
D. Insulation and Housing
Insulation is essential for ensuring the safety and reliability of NPRs. Different types of insulation materials are used, depending on the application and environmental conditions. The housing design is also crucial, as it must provide durability and protection against external factors such as moisture and temperature fluctuations.
E. Quality Assurance and Testing
Quality assurance is a critical component of the manufacturing process. Various testing methods are employed to ensure that NPRs meet industry standards. Electrical testing methods assess the performance of the resistive elements, while mechanical and thermal testing evaluate the durability and stability of the components. Compliance with industry standards is essential for ensuring the safety and reliability of NPRs in electrical systems.
V. Innovations in NPR Manufacturing
A. Advances in Materials Science
Recent advancements in materials science have led to the development of new conductive and insulating materials that enhance the performance of NPRs. These innovations allow for improved thermal management, increased resistance stability, and greater overall efficiency.
B. Automation and Industry 4.0
The integration of automation and Industry 4.0 technologies is transforming the manufacturing landscape. Robotics and artificial intelligence are increasingly being used to streamline production processes, reduce labor costs, and improve precision. This shift towards automation is enabling manufacturers to produce NPRs more efficiently and at a lower cost.
C. Sustainability Practices
Sustainability is becoming a key focus in NPR manufacturing. Manufacturers are adopting eco-friendly materials and processes to minimize their environmental impact. This includes implementing recycling programs and waste management strategies to reduce the overall carbon footprint of production.
VI. Challenges in NPR Manufacturing
A. Technical Challenges
Despite advancements in manufacturing processes, several technical challenges remain. Achieving precision in resistance values is critical, as even minor deviations can impact the performance of electrical systems. Additionally, managing thermal performance is essential to prevent overheating and ensure the longevity of NPRs.
B. Market Challenges
The NPR manufacturing market faces several challenges, including competition and pricing pressures. As demand for NPRs fluctuates, manufacturers must adapt to changing market conditions while maintaining quality and performance. This requires a keen understanding of market trends and customer needs.
VII. Future Trends in NPR Manufacturing
A. Emerging Technologies
The future of NPR manufacturing is likely to be shaped by emerging technologies, such as smart resistors and IoT integration. These innovations will enable NPRs to communicate with other devices, providing real-time data on performance and conditions. This connectivity will enhance the overall efficiency and reliability of electrical systems.
B. Market Growth and Opportunities
The market for NPRs is expected to grow significantly, driven by the expansion of renewable energy applications and innovations in electric vehicle technology. As the demand for efficient and reliable electrical solutions increases, manufacturers will have ample opportunities to develop and market advanced NPRs.
VIII. Conclusion
In summary, the manufacturing processes of the latest Neutral Point Resistors involve a complex interplay of design, material selection, fabrication techniques, and quality assurance. As the demand for efficient electrical solutions continues to rise, ongoing research and development in NPR manufacturing will be essential. The future of NPRs in electrical systems looks promising, with innovations in materials, automation, and sustainability paving the way for enhanced performance and reliability. As we move forward, the importance of NPRs in ensuring the stability and safety of electrical systems cannot be overstated.
Manufacturing Processes of the Latest Neutral Point Resistors
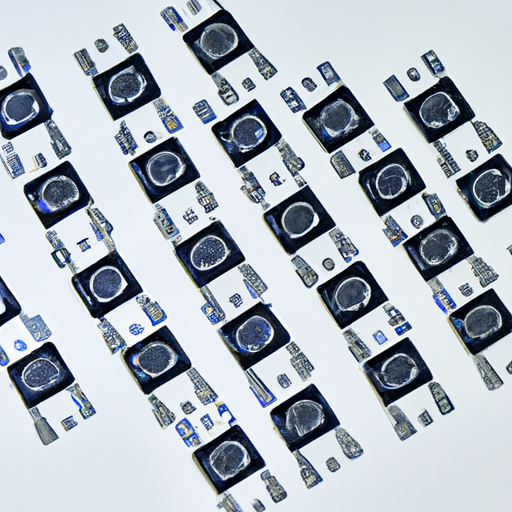
I. Introduction
Neutral Point Resistors (NPRs) are critical components in modern electrical systems, particularly in applications involving power electronics and renewable energy. These resistors play a vital role in managing voltage levels and ensuring the stability of electrical systems. As the demand for efficient and reliable electrical solutions grows, understanding the manufacturing processes of the latest NPRs becomes increasingly important. This blog post will explore the various stages involved in the production of NPRs, from raw material selection to innovative manufacturing techniques.
II. Understanding Neutral Point Resistors
A. Function and Application of NPRs
NPRs serve a crucial function in electrical systems by providing a path for fault currents to flow, thereby protecting sensitive equipment from damage. They are commonly used in power electronics, such as inverters and converters, where they help maintain voltage balance and prevent overvoltage conditions. Additionally, NPRs are integral to renewable energy systems, including wind and solar power installations, where they ensure the safe operation of electrical grids.
B. Types of Neutral Point Resistors
NPRs can be categorized into two main types: fixed resistors and variable resistors. Fixed NPRs have a predetermined resistance value, making them suitable for applications where consistent performance is required. In contrast, variable NPRs allow for adjustable resistance, providing flexibility in applications where conditions may change.
C. Key Specifications and Performance Metrics
When evaluating NPRs, several key specifications and performance metrics must be considered, including resistance value, power rating, thermal stability, and response time. These factors determine how effectively an NPR can perform its intended function in various electrical systems.
III. Raw Materials for NPR Manufacturing
A. Types of Materials Used
The manufacturing of NPRs involves a variety of raw materials. Conductive materials, such as carbon and metal alloys, are essential for creating the resistive elements. These materials must possess specific electrical properties to ensure optimal performance. Insulating materials, including ceramics and polymers, are also crucial for preventing electrical leakage and ensuring safety.
B. Quality Control of Raw Materials
Quality control is a vital aspect of the manufacturing process. Raw materials must be thoroughly tested to ensure they meet the required specifications. This includes assessing their electrical conductivity, thermal properties, and mechanical strength. Ensuring high-quality materials is essential for the reliability and longevity of the final product.
C. Environmental Considerations in Material Selection
In recent years, there has been a growing emphasis on sustainability in manufacturing. Manufacturers are increasingly selecting eco-friendly materials and processes to minimize their environmental impact. This includes using recyclable materials and reducing waste during production.
IV. Manufacturing Processes
A. Design and Prototyping
The manufacturing process begins with design and prototyping. Computer-aided design (CAD) tools are employed to create detailed models of NPRs. These models allow engineers to simulate and test various designs before moving to production. This stage is crucial for identifying potential issues and optimizing the design for performance and manufacturability.
B. Fabrication Techniques
Once the design is finalized, fabrication techniques come into play. This involves cutting and shaping the raw materials to create the various components of the NPR. Advanced machining techniques, such as laser cutting and CNC machining, are often used to achieve precise dimensions and tolerances.
C. Resistance Element Production
The production of the resistive elements is a critical step in the manufacturing process. Various methods are employed to create these elements, including sintering, where powdered materials are heated to form a solid mass. Techniques for achieving desired resistance values may involve adjusting the composition of the materials or altering the dimensions of the resistive elements.
D. Insulation and Housing
Insulation is essential for ensuring the safety and reliability of NPRs. Different types of insulation materials are used, depending on the application and environmental conditions. The housing design is also crucial, as it must provide durability and protection against external factors such as moisture and temperature fluctuations.
E. Quality Assurance and Testing
Quality assurance is a critical component of the manufacturing process. Various testing methods are employed to ensure that NPRs meet industry standards. Electrical testing methods assess the performance of the resistive elements, while mechanical and thermal testing evaluate the durability and stability of the components. Compliance with industry standards is essential for ensuring the safety and reliability of NPRs in electrical systems.
V. Innovations in NPR Manufacturing
A. Advances in Materials Science
Recent advancements in materials science have led to the development of new conductive and insulating materials that enhance the performance of NPRs. These innovations allow for improved thermal management, increased resistance stability, and greater overall efficiency.
B. Automation and Industry 4.0
The integration of automation and Industry 4.0 technologies is transforming the manufacturing landscape. Robotics and artificial intelligence are increasingly being used to streamline production processes, reduce labor costs, and improve precision. This shift towards automation is enabling manufacturers to produce NPRs more efficiently and at a lower cost.
C. Sustainability Practices
Sustainability is becoming a key focus in NPR manufacturing. Manufacturers are adopting eco-friendly materials and processes to minimize their environmental impact. This includes implementing recycling programs and waste management strategies to reduce the overall carbon footprint of production.
VI. Challenges in NPR Manufacturing
A. Technical Challenges
Despite advancements in manufacturing processes, several technical challenges remain. Achieving precision in resistance values is critical, as even minor deviations can impact the performance of electrical systems. Additionally, managing thermal performance is essential to prevent overheating and ensure the longevity of NPRs.
B. Market Challenges
The NPR manufacturing market faces several challenges, including competition and pricing pressures. As demand for NPRs fluctuates, manufacturers must adapt to changing market conditions while maintaining quality and performance. This requires a keen understanding of market trends and customer needs.
VII. Future Trends in NPR Manufacturing
A. Emerging Technologies
The future of NPR manufacturing is likely to be shaped by emerging technologies, such as smart resistors and IoT integration. These innovations will enable NPRs to communicate with other devices, providing real-time data on performance and conditions. This connectivity will enhance the overall efficiency and reliability of electrical systems.
B. Market Growth and Opportunities
The market for NPRs is expected to grow significantly, driven by the expansion of renewable energy applications and innovations in electric vehicle technology. As the demand for efficient and reliable electrical solutions increases, manufacturers will have ample opportunities to develop and market advanced NPRs.
VIII. Conclusion
In summary, the manufacturing processes of the latest Neutral Point Resistors involve a complex interplay of design, material selection, fabrication techniques, and quality assurance. As the demand for efficient electrical solutions continues to rise, ongoing research and development in NPR manufacturing will be essential. The future of NPRs in electrical systems looks promising, with innovations in materials, automation, and sustainability paving the way for enhanced performance and reliability. As we move forward, the importance of NPRs in ensuring the stability and safety of electrical systems cannot be overstated.