What are the Product Standards for Capacitor Films?
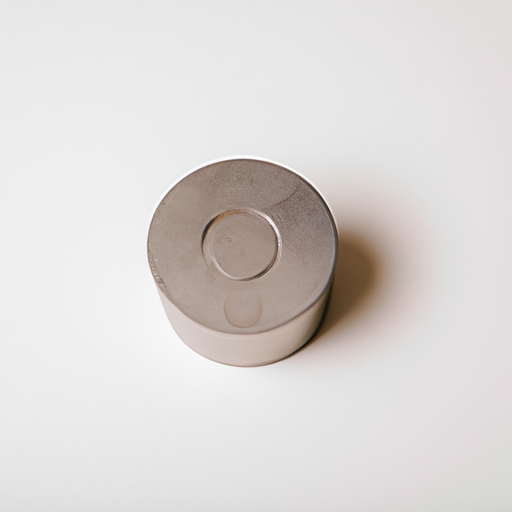
I. Introduction
Capacitor films are essential components in a wide range of electronic devices, serving as the dielectric material in capacitors that store and release electrical energy. These films are crucial for the performance and reliability of capacitors, which are used in everything from consumer electronics to industrial machinery. Given their importance, product standards for capacitor films play a vital role in ensuring safety, reliability, and quality in the electronics industry. This article will explore the various types of capacitor films, the significance of product standards, key organizations involved in standardization, and the specific standards that govern capacitor films.
II. Understanding Capacitor Films
A. Types of Capacitor Films
Capacitor films are made from various materials, each offering unique properties that make them suitable for different applications. The most common types include:
1. **Polyester (PET)**: Known for its excellent electrical properties and cost-effectiveness, polyester films are widely used in consumer electronics and general-purpose capacitors.
2. **Polypropylene (PP)**: This type of film is favored for its high insulation resistance and low dielectric losses, making it ideal for high-frequency applications and power electronics.
3. **Polycarbonate (PC)**: Polycarbonate films offer superior thermal stability and are often used in applications requiring high reliability, such as automotive and aerospace.
4. **Other materials**: Other films, such as polyimide and fluoropolymer, are also used in specialized applications where extreme conditions are present.
B. Applications of Capacitor Films
Capacitor films find applications across various sectors, including:
1. **Consumer electronics**: Used in devices like smartphones, televisions, and computers, capacitor films help manage power supply and signal processing.
2. **Industrial applications**: In manufacturing and automation, capacitor films are used in motor drives, power supplies, and control systems.
3. **Automotive uses**: Capacitor films are critical in electric vehicles and advanced driver-assistance systems (ADAS), where reliability and performance are paramount.
4. **Renewable energy systems**: In solar inverters and wind turbines, capacitor films help optimize energy conversion and storage.
III. Importance of Product Standards
Product standards for capacitor films are essential for several reasons:
A. Ensuring Safety and Reliability
Standards help ensure that capacitor films can withstand the electrical and environmental stresses they encounter in real-world applications. This is crucial for preventing failures that could lead to safety hazards.
B. Facilitating International Trade
With globalization, products are often manufactured in one country and sold in another. Standardization helps ensure that capacitor films meet the necessary requirements for different markets, facilitating smoother international trade.
C. Promoting Innovation and Quality Assurance
Standards encourage manufacturers to innovate while maintaining quality. By adhering to established benchmarks, companies can improve their products and processes, leading to better performance and reliability.
D. Protecting Consumers and Manufacturers
Standards protect consumers by ensuring that products are safe and reliable. They also protect manufacturers by providing a clear framework for compliance, reducing the risk of liability and recalls.
IV. Key Organizations and Standards
Several organizations play a crucial role in establishing and maintaining product standards for capacitor films:
A. International Electrotechnical Commission (IEC)
The IEC develops international standards for electrical and electronic technologies. Specific IEC standards for capacitor films address performance, safety, and testing methods.
B. Institute of Electrical and Electronics Engineers (IEEE)
IEEE is a leading organization in setting standards for electrical and electronic systems. Their standards for capacitors focus on performance metrics and testing procedures.
C. Underwriters Laboratories (UL)
UL is known for its rigorous safety testing and certification processes. UL standards for capacitor films ensure that products meet safety requirements, particularly in consumer electronics.
D. Other Relevant Organizations
1. **American National Standards Institute (ANSI)**: ANSI oversees the development of voluntary consensus standards for various industries, including electronics.
2. **European Committee for Electrotechnical Standardization (CENELEC)**: CENELEC develops standards for electrical and electronic products in Europe, ensuring compatibility and safety.
V. Key Product Standards for Capacitor Films
A. Electrical Characteristics
1. **Capacitance Tolerance**: This standard defines the acceptable range of capacitance values for a given capacitor film, ensuring consistent performance.
2. **Voltage Rating**: Capacitor films must be rated for specific voltage levels to prevent breakdown and failure.
3. **Temperature Coefficient**: This standard measures how capacitance changes with temperature, which is critical for applications in varying environmental conditions.
B. Mechanical Properties
1. **Thickness and Dimensional Tolerances**: Standards specify acceptable thickness ranges and dimensional tolerances to ensure compatibility with manufacturing processes.
2. **Tensile Strength and Elongation**: These properties determine the film's ability to withstand mechanical stress without breaking.
3. **Resistance to Environmental Factors**: Standards address how capacitor films perform under humidity, temperature fluctuations, and other environmental stresses.
C. Thermal Properties
1. **Thermal Stability**: This standard ensures that capacitor films maintain their properties at elevated temperatures.
2. **Insulation Resistance**: High insulation resistance is crucial for preventing electrical leakage and ensuring safety.
D. Safety and Compliance Standards
1. **Flammability Ratings**: Standards assess the flammability of capacitor films, ensuring they meet safety requirements.
2. **RoHS Compliance**: The Restriction of Hazardous Substances (RoHS) directive limits the use of specific hazardous materials in electronic products.
3. **REACH Regulations**: The Registration, Evaluation, Authorisation, and Restriction of Chemicals (REACH) regulations ensure that chemicals used in capacitor films are safe for human health and the environment.
VI. Testing and Quality Assurance
A. Overview of Testing Methods for Capacitor Films
1. **Electrical Testing**: This includes measuring capacitance, voltage rating, and insulation resistance to ensure compliance with electrical standards.
2. **Mechanical Testing**: Tests for tensile strength, elongation, and dimensional tolerances are conducted to assess the mechanical properties of the films.
3. **Environmental Testing**: Capacitor films are subjected to various environmental conditions to evaluate their performance and durability.
B. Importance of Quality Assurance in Manufacturing
Quality assurance processes are essential for maintaining product consistency and reliability. Manufacturers must implement rigorous testing and inspection protocols to ensure that capacitor films meet established standards.
C. Role of Third-Party Testing and Certification
Third-party testing organizations provide unbiased assessments of capacitor films, ensuring compliance with industry standards. Certification from recognized organizations enhances product credibility and market acceptance.
VII. Challenges in Meeting Product Standards
A. Evolving Technology and Materials
As technology advances, new materials and manufacturing processes emerge, posing challenges for standardization. Keeping standards up-to-date with technological advancements is crucial for ensuring relevance.
B. Globalization and Varying Standards Across Regions
Different regions may have varying standards, complicating compliance for manufacturers operating in multiple markets. Harmonizing standards can help mitigate these challenges.
C. Balancing Cost and Compliance
Manufacturers often face the challenge of balancing the costs associated with compliance and quality assurance with the need to remain competitive in the market.
VIII. Future Trends in Capacitor Film Standards
A. Innovations in Materials and Technology
The development of new materials, such as biodegradable films and advanced polymers, is expected to influence future standards for capacitor films.
B. Increasing Focus on Sustainability and Environmental Impact
As sustainability becomes a priority, standards will likely evolve to address environmental concerns, including the use of recyclable materials and reduced energy consumption in manufacturing.
C. Anticipated Changes in Regulatory Frameworks
Regulatory frameworks are expected to adapt to emerging technologies and materials, necessitating ongoing collaboration between industry stakeholders and standardization organizations.
IX. Conclusion
Product standards for capacitor films are essential for ensuring safety, reliability, and quality in the electronics industry. These standards not only protect consumers but also promote innovation and facilitate international trade. As technology continues to evolve, it is crucial for manufacturers and stakeholders to prioritize compliance with established standards while embracing innovation. By doing so, they can contribute to a safer, more efficient, and sustainable future for electronic components.
X. References
- International Electrotechnical Commission (IEC) Standards
- Institute of Electrical and Electronics Engineers (IEEE) Standards
- Underwriters Laboratories (UL) Certification Guidelines
- American National Standards Institute (ANSI) Publications
- European Committee for Electrotechnical Standardization (CENELEC) Standards
For further reading on capacitor films and product standards, consider exploring industry publications and technical journals that focus on advancements in materials and manufacturing processes.
What are the Product Standards for Capacitor Films?
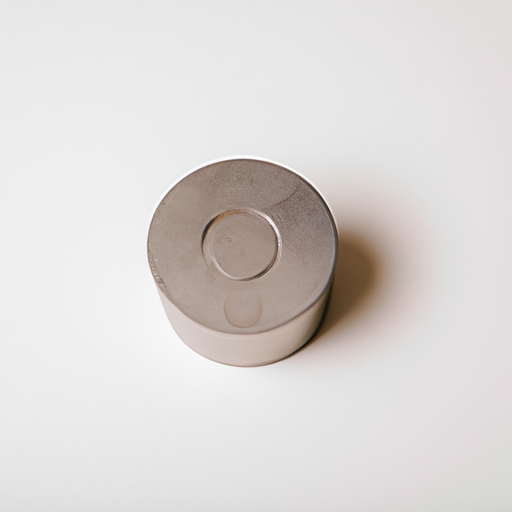
I. Introduction
Capacitor films are essential components in a wide range of electronic devices, serving as the dielectric material in capacitors that store and release electrical energy. These films are crucial for the performance and reliability of capacitors, which are used in everything from consumer electronics to industrial machinery. Given their importance, product standards for capacitor films play a vital role in ensuring safety, reliability, and quality in the electronics industry. This article will explore the various types of capacitor films, the significance of product standards, key organizations involved in standardization, and the specific standards that govern capacitor films.
II. Understanding Capacitor Films
A. Types of Capacitor Films
Capacitor films are made from various materials, each offering unique properties that make them suitable for different applications. The most common types include:
1. **Polyester (PET)**: Known for its excellent electrical properties and cost-effectiveness, polyester films are widely used in consumer electronics and general-purpose capacitors.
2. **Polypropylene (PP)**: This type of film is favored for its high insulation resistance and low dielectric losses, making it ideal for high-frequency applications and power electronics.
3. **Polycarbonate (PC)**: Polycarbonate films offer superior thermal stability and are often used in applications requiring high reliability, such as automotive and aerospace.
4. **Other materials**: Other films, such as polyimide and fluoropolymer, are also used in specialized applications where extreme conditions are present.
B. Applications of Capacitor Films
Capacitor films find applications across various sectors, including:
1. **Consumer electronics**: Used in devices like smartphones, televisions, and computers, capacitor films help manage power supply and signal processing.
2. **Industrial applications**: In manufacturing and automation, capacitor films are used in motor drives, power supplies, and control systems.
3. **Automotive uses**: Capacitor films are critical in electric vehicles and advanced driver-assistance systems (ADAS), where reliability and performance are paramount.
4. **Renewable energy systems**: In solar inverters and wind turbines, capacitor films help optimize energy conversion and storage.
III. Importance of Product Standards
Product standards for capacitor films are essential for several reasons:
A. Ensuring Safety and Reliability
Standards help ensure that capacitor films can withstand the electrical and environmental stresses they encounter in real-world applications. This is crucial for preventing failures that could lead to safety hazards.
B. Facilitating International Trade
With globalization, products are often manufactured in one country and sold in another. Standardization helps ensure that capacitor films meet the necessary requirements for different markets, facilitating smoother international trade.
C. Promoting Innovation and Quality Assurance
Standards encourage manufacturers to innovate while maintaining quality. By adhering to established benchmarks, companies can improve their products and processes, leading to better performance and reliability.
D. Protecting Consumers and Manufacturers
Standards protect consumers by ensuring that products are safe and reliable. They also protect manufacturers by providing a clear framework for compliance, reducing the risk of liability and recalls.
IV. Key Organizations and Standards
Several organizations play a crucial role in establishing and maintaining product standards for capacitor films:
A. International Electrotechnical Commission (IEC)
The IEC develops international standards for electrical and electronic technologies. Specific IEC standards for capacitor films address performance, safety, and testing methods.
B. Institute of Electrical and Electronics Engineers (IEEE)
IEEE is a leading organization in setting standards for electrical and electronic systems. Their standards for capacitors focus on performance metrics and testing procedures.
C. Underwriters Laboratories (UL)
UL is known for its rigorous safety testing and certification processes. UL standards for capacitor films ensure that products meet safety requirements, particularly in consumer electronics.
D. Other Relevant Organizations
1. **American National Standards Institute (ANSI)**: ANSI oversees the development of voluntary consensus standards for various industries, including electronics.
2. **European Committee for Electrotechnical Standardization (CENELEC)**: CENELEC develops standards for electrical and electronic products in Europe, ensuring compatibility and safety.
V. Key Product Standards for Capacitor Films
A. Electrical Characteristics
1. **Capacitance Tolerance**: This standard defines the acceptable range of capacitance values for a given capacitor film, ensuring consistent performance.
2. **Voltage Rating**: Capacitor films must be rated for specific voltage levels to prevent breakdown and failure.
3. **Temperature Coefficient**: This standard measures how capacitance changes with temperature, which is critical for applications in varying environmental conditions.
B. Mechanical Properties
1. **Thickness and Dimensional Tolerances**: Standards specify acceptable thickness ranges and dimensional tolerances to ensure compatibility with manufacturing processes.
2. **Tensile Strength and Elongation**: These properties determine the film's ability to withstand mechanical stress without breaking.
3. **Resistance to Environmental Factors**: Standards address how capacitor films perform under humidity, temperature fluctuations, and other environmental stresses.
C. Thermal Properties
1. **Thermal Stability**: This standard ensures that capacitor films maintain their properties at elevated temperatures.
2. **Insulation Resistance**: High insulation resistance is crucial for preventing electrical leakage and ensuring safety.
D. Safety and Compliance Standards
1. **Flammability Ratings**: Standards assess the flammability of capacitor films, ensuring they meet safety requirements.
2. **RoHS Compliance**: The Restriction of Hazardous Substances (RoHS) directive limits the use of specific hazardous materials in electronic products.
3. **REACH Regulations**: The Registration, Evaluation, Authorisation, and Restriction of Chemicals (REACH) regulations ensure that chemicals used in capacitor films are safe for human health and the environment.
VI. Testing and Quality Assurance
A. Overview of Testing Methods for Capacitor Films
1. **Electrical Testing**: This includes measuring capacitance, voltage rating, and insulation resistance to ensure compliance with electrical standards.
2. **Mechanical Testing**: Tests for tensile strength, elongation, and dimensional tolerances are conducted to assess the mechanical properties of the films.
3. **Environmental Testing**: Capacitor films are subjected to various environmental conditions to evaluate their performance and durability.
B. Importance of Quality Assurance in Manufacturing
Quality assurance processes are essential for maintaining product consistency and reliability. Manufacturers must implement rigorous testing and inspection protocols to ensure that capacitor films meet established standards.
C. Role of Third-Party Testing and Certification
Third-party testing organizations provide unbiased assessments of capacitor films, ensuring compliance with industry standards. Certification from recognized organizations enhances product credibility and market acceptance.
VII. Challenges in Meeting Product Standards
A. Evolving Technology and Materials
As technology advances, new materials and manufacturing processes emerge, posing challenges for standardization. Keeping standards up-to-date with technological advancements is crucial for ensuring relevance.
B. Globalization and Varying Standards Across Regions
Different regions may have varying standards, complicating compliance for manufacturers operating in multiple markets. Harmonizing standards can help mitigate these challenges.
C. Balancing Cost and Compliance
Manufacturers often face the challenge of balancing the costs associated with compliance and quality assurance with the need to remain competitive in the market.
VIII. Future Trends in Capacitor Film Standards
A. Innovations in Materials and Technology
The development of new materials, such as biodegradable films and advanced polymers, is expected to influence future standards for capacitor films.
B. Increasing Focus on Sustainability and Environmental Impact
As sustainability becomes a priority, standards will likely evolve to address environmental concerns, including the use of recyclable materials and reduced energy consumption in manufacturing.
C. Anticipated Changes in Regulatory Frameworks
Regulatory frameworks are expected to adapt to emerging technologies and materials, necessitating ongoing collaboration between industry stakeholders and standardization organizations.
IX. Conclusion
Product standards for capacitor films are essential for ensuring safety, reliability, and quality in the electronics industry. These standards not only protect consumers but also promote innovation and facilitate international trade. As technology continues to evolve, it is crucial for manufacturers and stakeholders to prioritize compliance with established standards while embracing innovation. By doing so, they can contribute to a safer, more efficient, and sustainable future for electronic components.
X. References
- International Electrotechnical Commission (IEC) Standards
- Institute of Electrical and Electronics Engineers (IEEE) Standards
- Underwriters Laboratories (UL) Certification Guidelines
- American National Standards Institute (ANSI) Publications
- European Committee for Electrotechnical Standardization (CENELEC) Standards
For further reading on capacitor films and product standards, consider exploring industry publications and technical journals that focus on advancements in materials and manufacturing processes.