What is the Mainstream Production Process of Parallel Capacitors?
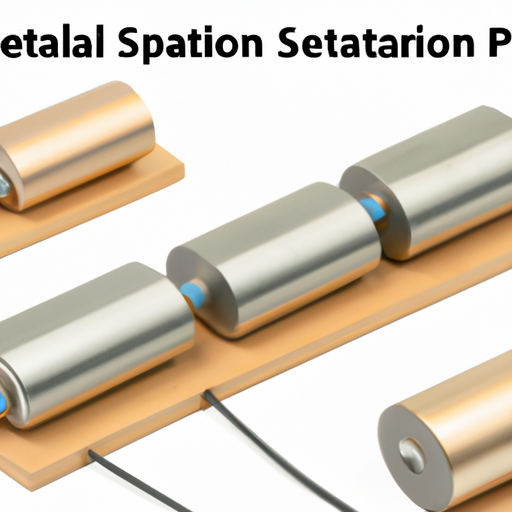
I. Introduction
A. Definition of Parallel Capacitors
Parallel capacitors are capacitors connected in such a way that they share the same voltage across their terminals. This configuration allows for an increase in the total capacitance, which is the sum of the individual capacitances. In electronic circuits, parallel capacitors are often used to enhance performance, improve stability, and filter out noise.
B. Importance of Capacitors in Electronic Circuits
Capacitors play a crucial role in electronic circuits, serving various functions such as energy storage, voltage smoothing, and signal filtering. They are essential components in power supply circuits, audio equipment, and timing applications. The ability to combine capacitors in parallel allows designers to achieve desired capacitance values while optimizing circuit performance.
C. Overview of the Production Process
The production of parallel capacitors involves several stages, from material selection to manufacturing and quality assurance. Understanding this process is vital for appreciating the complexity and precision required in capacitor manufacturing.
II. Types of Capacitors
A. Electrolytic Capacitors
Electrolytic capacitors are polarized capacitors that use an electrolyte as one of their plates. They are known for their high capacitance values and are commonly used in power supply applications.
B. Ceramic Capacitors
Ceramic capacitors are non-polarized capacitors made from ceramic materials. They are widely used due to their stability, reliability, and small size, making them ideal for high-frequency applications.
C. Film Capacitors
Film capacitors use a thin plastic film as the dielectric. They are known for their excellent performance in terms of stability and low loss, making them suitable for audio and high-frequency applications.
D. Tantalum Capacitors
Tantalum capacitors are another type of electrolytic capacitor, known for their small size and high capacitance. They are often used in applications where space is limited, such as in mobile devices.
E. Comparison of Different Types
Each type of capacitor has its advantages and disadvantages, making them suitable for different applications. Electrolytic capacitors offer high capacitance but are polarized, while ceramic capacitors are non-polarized and stable but have lower capacitance values. Understanding these differences is essential for selecting the right capacitor for a specific application.
III. Raw Materials Used in Capacitor Production
A. Dielectric Materials
1. Types of Dielectrics
The dielectric material is a crucial component of capacitors, as it separates the conductive plates and stores electrical energy. Common dielectric materials include ceramic, plastic film, and electrolytic solutions.
2. Properties Required for Dielectrics
Dielectric materials must possess high insulation resistance, low dielectric loss, and stability over a range of temperatures and frequencies. These properties ensure that the capacitor performs reliably in various conditions.
B. Conductive Materials
1. Types of Conductors
Conductive materials, typically metals like aluminum or tantalum, form the plates of the capacitor. The choice of conductor affects the capacitor's performance, including its equivalent series resistance (ESR) and overall efficiency.
2. Importance of Conductive Materials
The quality of conductive materials is vital for ensuring low resistance and high reliability in capacitors. Poor-quality conductors can lead to increased heat generation and reduced lifespan.
C. Other Components
1. Leads and Terminals
Leads and terminals are essential for connecting capacitors to circuits. They must be made from conductive materials and designed to withstand mechanical stress and thermal expansion.
2. Encapsulation Materials
Encapsulation materials protect the capacitor from environmental factors such as moisture and dust. They also provide mechanical support and enhance the overall durability of the capacitor.
IV. The Production Process
A. Design and Engineering
1. Specifications and Requirements
The production process begins with design and engineering, where specifications for the capacitor are established. This includes determining capacitance values, voltage ratings, and physical dimensions.
2. Prototyping and Testing
Once the design is finalized, prototypes are created and tested to ensure they meet the required specifications. This stage is critical for identifying potential issues before mass production.
B. Material Preparation
1. Sourcing Raw Materials
Raw materials are sourced from suppliers, ensuring they meet quality standards. This includes dielectric materials, conductive materials, and encapsulation components.
2. Quality Control of Materials
Quality control measures are implemented to verify the integrity of the raw materials. This step is essential for ensuring that the final product meets performance and safety standards.
C. Manufacturing Steps
1. Dielectric Layer Formation
The first step in manufacturing capacitors is forming the dielectric layer. This can be achieved through various methods, including deposition and layering techniques. The choice of method depends on the type of capacitor being produced.
2. Electrode Formation
Electrode formation involves creating the conductive plates of the capacitor. Techniques such as sputtering and etching are commonly used to achieve the desired thickness and surface area.
3. Assembly of Components
Once the dielectric and electrodes are prepared, the components are assembled. This includes layering and stacking the dielectric and electrodes, followed by connecting the leads.
4. Encapsulation and Sealing
The final assembly step involves encapsulating and sealing the capacitor. Different types of encapsulation materials are used, depending on the application and environmental requirements. Proper sealing is crucial for protecting the capacitor from moisture and contaminants.
D. Quality Assurance
1. Testing Procedures
After production, capacitors undergo rigorous testing to ensure they meet performance specifications. This includes electrical testing, thermal testing, and mechanical stress testing.
2. Compliance with Standards
Manufacturers must comply with industry standards and regulations, such as those set by the International Electrotechnical Commission (IEC) and the American National Standards Institute (ANSI). Compliance ensures that the capacitors are safe and reliable for use in electronic circuits.
V. Environmental Considerations
A. Sustainable Practices in Production
As environmental concerns grow, manufacturers are adopting sustainable practices in capacitor production. This includes using eco-friendly materials, reducing waste, and minimizing energy consumption during manufacturing.
B. Recycling and Disposal of Capacitors
Proper recycling and disposal of capacitors are essential to prevent environmental contamination. Many manufacturers are implementing take-back programs to ensure that old capacitors are disposed of responsibly.
C. Regulatory Compliance
Manufacturers must adhere to environmental regulations, such as the Restriction of Hazardous Substances (RoHS) directive, which limits the use of certain hazardous materials in electronic products.
VI. Conclusion
A. Summary of the Production Process
The production process of parallel capacitors involves several critical stages, from design and material preparation to manufacturing and quality assurance. Each step is essential for ensuring that the final product meets performance and safety standards.
B. Future Trends in Capacitor Manufacturing
As technology advances, the demand for smaller, more efficient capacitors continues to grow. Future trends may include the development of new materials, improved manufacturing techniques, and enhanced recycling processes.
C. The Role of Parallel Capacitors in Advancing Technology
Parallel capacitors play a vital role in modern electronic circuits, enabling the development of advanced technologies in various fields, including telecommunications, automotive, and consumer electronics. Their importance will only continue to grow as technology evolves.
VII. References
A. Academic Journals
- Journal of Applied Physics
- IEEE Transactions on Electron Devices
B. Industry Reports
- Capacitor Market Analysis Report
- Global Electronics Industry Trends
C. Manufacturer Guidelines
- Capacitor Manufacturing Best Practices
- Quality Assurance Standards for Capacitors
---
This blog post provides a comprehensive overview of the mainstream production process of parallel capacitors, highlighting the importance of each stage and the materials involved. Understanding this process is essential for anyone interested in electronics and capacitor technology.
What is the Mainstream Production Process of Parallel Capacitors?
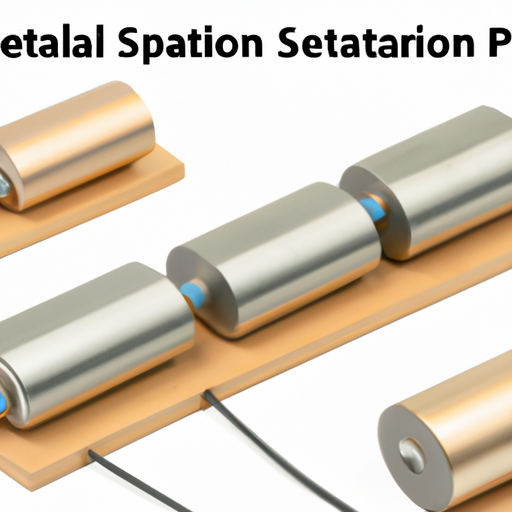
I. Introduction
A. Definition of Parallel Capacitors
Parallel capacitors are capacitors connected in such a way that they share the same voltage across their terminals. This configuration allows for an increase in the total capacitance, which is the sum of the individual capacitances. In electronic circuits, parallel capacitors are often used to enhance performance, improve stability, and filter out noise.
B. Importance of Capacitors in Electronic Circuits
Capacitors play a crucial role in electronic circuits, serving various functions such as energy storage, voltage smoothing, and signal filtering. They are essential components in power supply circuits, audio equipment, and timing applications. The ability to combine capacitors in parallel allows designers to achieve desired capacitance values while optimizing circuit performance.
C. Overview of the Production Process
The production of parallel capacitors involves several stages, from material selection to manufacturing and quality assurance. Understanding this process is vital for appreciating the complexity and precision required in capacitor manufacturing.
II. Types of Capacitors
A. Electrolytic Capacitors
Electrolytic capacitors are polarized capacitors that use an electrolyte as one of their plates. They are known for their high capacitance values and are commonly used in power supply applications.
B. Ceramic Capacitors
Ceramic capacitors are non-polarized capacitors made from ceramic materials. They are widely used due to their stability, reliability, and small size, making them ideal for high-frequency applications.
C. Film Capacitors
Film capacitors use a thin plastic film as the dielectric. They are known for their excellent performance in terms of stability and low loss, making them suitable for audio and high-frequency applications.
D. Tantalum Capacitors
Tantalum capacitors are another type of electrolytic capacitor, known for their small size and high capacitance. They are often used in applications where space is limited, such as in mobile devices.
E. Comparison of Different Types
Each type of capacitor has its advantages and disadvantages, making them suitable for different applications. Electrolytic capacitors offer high capacitance but are polarized, while ceramic capacitors are non-polarized and stable but have lower capacitance values. Understanding these differences is essential for selecting the right capacitor for a specific application.
III. Raw Materials Used in Capacitor Production
A. Dielectric Materials
1. Types of Dielectrics
The dielectric material is a crucial component of capacitors, as it separates the conductive plates and stores electrical energy. Common dielectric materials include ceramic, plastic film, and electrolytic solutions.
2. Properties Required for Dielectrics
Dielectric materials must possess high insulation resistance, low dielectric loss, and stability over a range of temperatures and frequencies. These properties ensure that the capacitor performs reliably in various conditions.
B. Conductive Materials
1. Types of Conductors
Conductive materials, typically metals like aluminum or tantalum, form the plates of the capacitor. The choice of conductor affects the capacitor's performance, including its equivalent series resistance (ESR) and overall efficiency.
2. Importance of Conductive Materials
The quality of conductive materials is vital for ensuring low resistance and high reliability in capacitors. Poor-quality conductors can lead to increased heat generation and reduced lifespan.
C. Other Components
1. Leads and Terminals
Leads and terminals are essential for connecting capacitors to circuits. They must be made from conductive materials and designed to withstand mechanical stress and thermal expansion.
2. Encapsulation Materials
Encapsulation materials protect the capacitor from environmental factors such as moisture and dust. They also provide mechanical support and enhance the overall durability of the capacitor.
IV. The Production Process
A. Design and Engineering
1. Specifications and Requirements
The production process begins with design and engineering, where specifications for the capacitor are established. This includes determining capacitance values, voltage ratings, and physical dimensions.
2. Prototyping and Testing
Once the design is finalized, prototypes are created and tested to ensure they meet the required specifications. This stage is critical for identifying potential issues before mass production.
B. Material Preparation
1. Sourcing Raw Materials
Raw materials are sourced from suppliers, ensuring they meet quality standards. This includes dielectric materials, conductive materials, and encapsulation components.
2. Quality Control of Materials
Quality control measures are implemented to verify the integrity of the raw materials. This step is essential for ensuring that the final product meets performance and safety standards.
C. Manufacturing Steps
1. Dielectric Layer Formation
The first step in manufacturing capacitors is forming the dielectric layer. This can be achieved through various methods, including deposition and layering techniques. The choice of method depends on the type of capacitor being produced.
2. Electrode Formation
Electrode formation involves creating the conductive plates of the capacitor. Techniques such as sputtering and etching are commonly used to achieve the desired thickness and surface area.
3. Assembly of Components
Once the dielectric and electrodes are prepared, the components are assembled. This includes layering and stacking the dielectric and electrodes, followed by connecting the leads.
4. Encapsulation and Sealing
The final assembly step involves encapsulating and sealing the capacitor. Different types of encapsulation materials are used, depending on the application and environmental requirements. Proper sealing is crucial for protecting the capacitor from moisture and contaminants.
D. Quality Assurance
1. Testing Procedures
After production, capacitors undergo rigorous testing to ensure they meet performance specifications. This includes electrical testing, thermal testing, and mechanical stress testing.
2. Compliance with Standards
Manufacturers must comply with industry standards and regulations, such as those set by the International Electrotechnical Commission (IEC) and the American National Standards Institute (ANSI). Compliance ensures that the capacitors are safe and reliable for use in electronic circuits.
V. Environmental Considerations
A. Sustainable Practices in Production
As environmental concerns grow, manufacturers are adopting sustainable practices in capacitor production. This includes using eco-friendly materials, reducing waste, and minimizing energy consumption during manufacturing.
B. Recycling and Disposal of Capacitors
Proper recycling and disposal of capacitors are essential to prevent environmental contamination. Many manufacturers are implementing take-back programs to ensure that old capacitors are disposed of responsibly.
C. Regulatory Compliance
Manufacturers must adhere to environmental regulations, such as the Restriction of Hazardous Substances (RoHS) directive, which limits the use of certain hazardous materials in electronic products.
VI. Conclusion
A. Summary of the Production Process
The production process of parallel capacitors involves several critical stages, from design and material preparation to manufacturing and quality assurance. Each step is essential for ensuring that the final product meets performance and safety standards.
B. Future Trends in Capacitor Manufacturing
As technology advances, the demand for smaller, more efficient capacitors continues to grow. Future trends may include the development of new materials, improved manufacturing techniques, and enhanced recycling processes.
C. The Role of Parallel Capacitors in Advancing Technology
Parallel capacitors play a vital role in modern electronic circuits, enabling the development of advanced technologies in various fields, including telecommunications, automotive, and consumer electronics. Their importance will only continue to grow as technology evolves.
VII. References
A. Academic Journals
- Journal of Applied Physics
- IEEE Transactions on Electron Devices
B. Industry Reports
- Capacitor Market Analysis Report
- Global Electronics Industry Trends
C. Manufacturer Guidelines
- Capacitor Manufacturing Best Practices
- Quality Assurance Standards for Capacitors
---
This blog post provides a comprehensive overview of the mainstream production process of parallel capacitors, highlighting the importance of each stage and the materials involved. Understanding this process is essential for anyone interested in electronics and capacitor technology.