Manufacturing Processes of the Latest Current Sensing Resistors
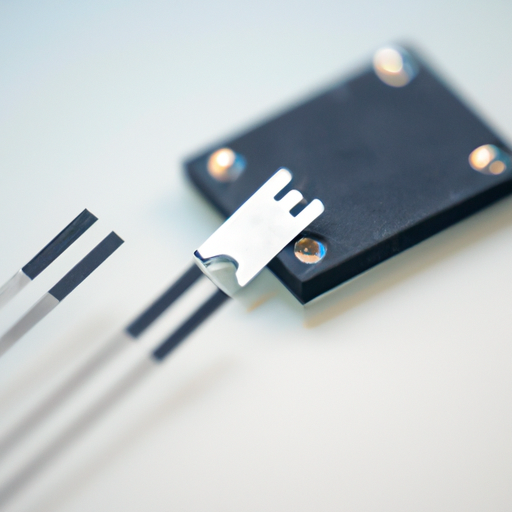
I. Introduction
A. Definition of Current Sensing Resistors
Current sensing resistors, often referred to as shunt resistors, are specialized components used to measure electric current in a circuit. They operate on the principle of Ohm's law, where the voltage drop across the resistor is proportional to the current flowing through it. These resistors are critical in various applications, including power management, automotive systems, and renewable energy technologies.
B. Importance of Current Sensing Resistors in Modern Electronics
In today's electronics landscape, the demand for precise current measurement is paramount. Current sensing resistors play a vital role in ensuring the efficiency and safety of electronic devices. They are integral to battery management systems, motor control, and energy monitoring applications, enabling real-time feedback and control. As the world moves towards more electrified systems, the importance of these components continues to grow.
C. Overview of the Manufacturing Process
The manufacturing of current sensing resistors involves several intricate processes, from material selection to fabrication and testing. This blog post will delve into the various types of current sensing resistors, the raw materials used, the manufacturing processes involved, innovations in the field, challenges faced, and future trends.
II. Types of Current Sensing Resistors
A. Thick Film Resistors
1. Composition and Characteristics
Thick film resistors are made by printing a resistive paste onto a substrate, typically ceramic. The paste consists of metal oxides and glass frit, which are fired at high temperatures to form a solid resistive layer. These resistors are known for their robustness and ability to handle high power levels.
2. Applications
Thick film resistors are widely used in power electronics, automotive applications, and industrial equipment due to their high power handling capabilities and cost-effectiveness.
B. Thin Film Resistors
1. Composition and Characteristics
Thin film resistors are created by depositing a thin layer of resistive material, such as nickel-chromium, onto a substrate using techniques like sputtering or chemical vapor deposition (CVD). They offer superior precision and stability compared to thick film resistors.
2. Applications
These resistors are ideal for applications requiring high accuracy and low temperature coefficients, such as precision measurement instruments and high-frequency circuits.
C. Wirewound Resistors
1. Composition and Characteristics
Wirewound resistors are constructed by winding a metal wire, typically made of nickel-chromium or copper-nickel alloy, around a ceramic or fiberglass core. This design allows for excellent heat dissipation and high power ratings.
2. Applications
Wirewound resistors are commonly used in power supplies, motor control circuits, and high-current applications due to their ability to handle significant power loads.
D. Shunt Resistors
1. Composition and Characteristics
Shunt resistors are specifically designed to measure current by providing a low-resistance path in a circuit. They are typically made from high-conductivity materials to minimize power loss.
2. Applications
Shunt resistors are extensively used in battery management systems, electric vehicles, and renewable energy systems for accurate current measurement.
III. Raw Materials Used in Manufacturing
A. Conductive Materials
1. Metal Alloys
Metal alloys, such as nickel-chromium and copper-nickel, are commonly used in the production of current sensing resistors due to their favorable electrical properties and stability.
2. Carbon-Based Materials
Carbon-based materials are also utilized, particularly in thick film resistors, where they provide a cost-effective solution with good thermal stability.
B. Substrates
1. Ceramic
Ceramic substrates are preferred for their excellent thermal and electrical insulation properties, making them ideal for high-power applications.
2. Epoxy
Epoxy substrates are used in applications where flexibility and lightweight characteristics are essential, such as in portable devices.
3. Other Materials
Other materials, including glass and metal, may also be used depending on the specific requirements of the resistor.
C. Protective Coatings
1. Insulating Materials
Insulating materials are applied to protect the resistors from environmental factors and to ensure safety in high-voltage applications.
2. Environmental Protection
Coatings that provide environmental protection are crucial for resistors used in harsh conditions, ensuring longevity and reliability.
IV. Manufacturing Processes
A. Design and Prototyping
1. Computer-Aided Design (CAD)
The manufacturing process begins with design and prototyping, where engineers use CAD software to create detailed designs of the resistors, ensuring precision and functionality.
2. Simulation and Testing
Before moving to production, simulations are conducted to predict the performance of the resistors under various conditions, allowing for adjustments to be made early in the process.
B. Material Preparation
1. Sourcing and Quality Control
Raw materials are sourced from reliable suppliers, and stringent quality control measures are implemented to ensure that they meet the required specifications.
2. Material Processing Techniques
Materials undergo various processing techniques, such as milling and mixing, to prepare them for the fabrication stage.
C. Fabrication Techniques
1. Thick Film Printing
a. Screen Printing
In thick film printing, a resistive paste is applied to the substrate using screen printing techniques, allowing for precise control over the thickness and pattern.
b. Inkjet Printing
Inkjet printing is an emerging technique that offers flexibility in design and can produce complex patterns with high resolution.
2. Thin Film Deposition
a. Sputtering
Sputtering is a physical vapor deposition technique used to create thin films of resistive materials on substrates, ensuring uniform thickness and composition.
b. Chemical Vapor Deposition (CVD)
CVD is another method for thin film deposition, where gaseous precursors react to form a solid film on the substrate, providing excellent control over material properties.
3. Wirewound Techniques
a. Winding Process
In wirewound resistor manufacturing, the winding process involves carefully wrapping the metal wire around a core to achieve the desired resistance value.
b. Termination
Termination involves connecting the wire ends to terminals, ensuring reliable electrical connections.
4. Shunt Resistor Fabrication
a. Cutting and Shaping
Shunt resistors are cut and shaped from larger blocks of conductive material, ensuring precise dimensions for accurate current measurement.
b. Soldering and Assembly
The final assembly involves soldering the shunt resistors onto circuit boards or connecting them to other components.
D. Testing and Quality Assurance
1. Electrical Testing
Each resistor undergoes rigorous electrical testing to verify its resistance value, tolerance, and performance under load conditions.
2. Environmental Testing
Environmental testing ensures that the resistors can withstand various conditions, such as temperature fluctuations and humidity.
3. Reliability Testing
Reliability testing assesses the long-term performance of the resistors, ensuring they meet industry standards and customer expectations.
V. Innovations in Current Sensing Resistor Manufacturing
A. Advances in Materials Science
1. Nanomaterials
The incorporation of nanomaterials in resistor manufacturing has led to improved performance characteristics, such as enhanced sensitivity and reduced size.
2. Composite Materials
Composite materials are being explored to create resistors with tailored properties, combining the benefits of different materials for optimal performance.
B. Automation and Industry 4.0
1. Smart Manufacturing Techniques
Automation in manufacturing processes has increased efficiency and precision, allowing for higher production rates and reduced costs.
2. Data Analytics in Production
Data analytics is being utilized to monitor production processes in real-time, enabling quick adjustments and improving overall quality.
C. Environmental Considerations
1. Sustainable Manufacturing Practices
Manufacturers are increasingly adopting sustainable practices, such as reducing waste and energy consumption, to minimize their environmental impact.
2. Recycling and Waste Management
Efforts are being made to recycle materials used in resistor production and manage waste effectively, contributing to a circular economy.
VI. Challenges in Manufacturing Current Sensing Resistors
A. Cost Management
Managing production costs while maintaining quality is a significant challenge for manufacturers, especially with fluctuating raw material prices.
B. Supply Chain Issues
Global supply chain disruptions can impact the availability of raw materials, leading to delays in production and increased costs.
C. Meeting Industry Standards and Regulations
Manufacturers must navigate complex industry standards and regulations, ensuring their products comply with safety and performance requirements.
VII. Future Trends in Current Sensing Resistor Manufacturing
A. Miniaturization and Integration
As electronic devices become smaller and more integrated, the demand for miniaturized current sensing resistors will continue to rise, driving innovation in manufacturing techniques.
B. Enhanced Performance Metrics
Future resistors will likely feature enhanced performance metrics, such as improved accuracy, lower power consumption, and greater thermal stability.
C. Emerging Applications in Electric Vehicles and Renewable Energy
The growing adoption of electric vehicles and renewable energy systems presents new opportunities for current sensing resistors, necessitating advancements in their design and manufacturing.
VIII. Conclusion
A. Summary of Key Points
Current sensing resistors are essential components in modern electronics, with various types and manufacturing processes that cater to diverse applications. The advancements in materials science, automation, and sustainable practices are shaping the future of resistor manufacturing.
B. The Role of Current Sensing Resistors in Future Technologies
As technology continues to evolve, the role of current sensing resistors will become increasingly critical in ensuring the efficiency and safety of electronic systems.
C. Final Thoughts on Manufacturing Innovations
The ongoing innovations in the manufacturing processes of current sensing resistors will not only enhance their performance but also contribute to the development of smarter, more sustainable electronic devices. As we look to the future, the importance of these components in driving technological advancements cannot be overstated.
Manufacturing Processes of the Latest Current Sensing Resistors
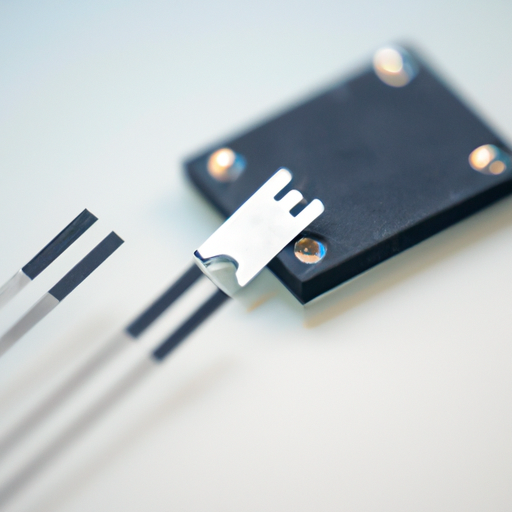
I. Introduction
A. Definition of Current Sensing Resistors
Current sensing resistors, often referred to as shunt resistors, are specialized components used to measure electric current in a circuit. They operate on the principle of Ohm's law, where the voltage drop across the resistor is proportional to the current flowing through it. These resistors are critical in various applications, including power management, automotive systems, and renewable energy technologies.
B. Importance of Current Sensing Resistors in Modern Electronics
In today's electronics landscape, the demand for precise current measurement is paramount. Current sensing resistors play a vital role in ensuring the efficiency and safety of electronic devices. They are integral to battery management systems, motor control, and energy monitoring applications, enabling real-time feedback and control. As the world moves towards more electrified systems, the importance of these components continues to grow.
C. Overview of the Manufacturing Process
The manufacturing of current sensing resistors involves several intricate processes, from material selection to fabrication and testing. This blog post will delve into the various types of current sensing resistors, the raw materials used, the manufacturing processes involved, innovations in the field, challenges faced, and future trends.
II. Types of Current Sensing Resistors
A. Thick Film Resistors
1. Composition and Characteristics
Thick film resistors are made by printing a resistive paste onto a substrate, typically ceramic. The paste consists of metal oxides and glass frit, which are fired at high temperatures to form a solid resistive layer. These resistors are known for their robustness and ability to handle high power levels.
2. Applications
Thick film resistors are widely used in power electronics, automotive applications, and industrial equipment due to their high power handling capabilities and cost-effectiveness.
B. Thin Film Resistors
1. Composition and Characteristics
Thin film resistors are created by depositing a thin layer of resistive material, such as nickel-chromium, onto a substrate using techniques like sputtering or chemical vapor deposition (CVD). They offer superior precision and stability compared to thick film resistors.
2. Applications
These resistors are ideal for applications requiring high accuracy and low temperature coefficients, such as precision measurement instruments and high-frequency circuits.
C. Wirewound Resistors
1. Composition and Characteristics
Wirewound resistors are constructed by winding a metal wire, typically made of nickel-chromium or copper-nickel alloy, around a ceramic or fiberglass core. This design allows for excellent heat dissipation and high power ratings.
2. Applications
Wirewound resistors are commonly used in power supplies, motor control circuits, and high-current applications due to their ability to handle significant power loads.
D. Shunt Resistors
1. Composition and Characteristics
Shunt resistors are specifically designed to measure current by providing a low-resistance path in a circuit. They are typically made from high-conductivity materials to minimize power loss.
2. Applications
Shunt resistors are extensively used in battery management systems, electric vehicles, and renewable energy systems for accurate current measurement.
III. Raw Materials Used in Manufacturing
A. Conductive Materials
1. Metal Alloys
Metal alloys, such as nickel-chromium and copper-nickel, are commonly used in the production of current sensing resistors due to their favorable electrical properties and stability.
2. Carbon-Based Materials
Carbon-based materials are also utilized, particularly in thick film resistors, where they provide a cost-effective solution with good thermal stability.
B. Substrates
1. Ceramic
Ceramic substrates are preferred for their excellent thermal and electrical insulation properties, making them ideal for high-power applications.
2. Epoxy
Epoxy substrates are used in applications where flexibility and lightweight characteristics are essential, such as in portable devices.
3. Other Materials
Other materials, including glass and metal, may also be used depending on the specific requirements of the resistor.
C. Protective Coatings
1. Insulating Materials
Insulating materials are applied to protect the resistors from environmental factors and to ensure safety in high-voltage applications.
2. Environmental Protection
Coatings that provide environmental protection are crucial for resistors used in harsh conditions, ensuring longevity and reliability.
IV. Manufacturing Processes
A. Design and Prototyping
1. Computer-Aided Design (CAD)
The manufacturing process begins with design and prototyping, where engineers use CAD software to create detailed designs of the resistors, ensuring precision and functionality.
2. Simulation and Testing
Before moving to production, simulations are conducted to predict the performance of the resistors under various conditions, allowing for adjustments to be made early in the process.
B. Material Preparation
1. Sourcing and Quality Control
Raw materials are sourced from reliable suppliers, and stringent quality control measures are implemented to ensure that they meet the required specifications.
2. Material Processing Techniques
Materials undergo various processing techniques, such as milling and mixing, to prepare them for the fabrication stage.
C. Fabrication Techniques
1. Thick Film Printing
a. Screen Printing
In thick film printing, a resistive paste is applied to the substrate using screen printing techniques, allowing for precise control over the thickness and pattern.
b. Inkjet Printing
Inkjet printing is an emerging technique that offers flexibility in design and can produce complex patterns with high resolution.
2. Thin Film Deposition
a. Sputtering
Sputtering is a physical vapor deposition technique used to create thin films of resistive materials on substrates, ensuring uniform thickness and composition.
b. Chemical Vapor Deposition (CVD)
CVD is another method for thin film deposition, where gaseous precursors react to form a solid film on the substrate, providing excellent control over material properties.
3. Wirewound Techniques
a. Winding Process
In wirewound resistor manufacturing, the winding process involves carefully wrapping the metal wire around a core to achieve the desired resistance value.
b. Termination
Termination involves connecting the wire ends to terminals, ensuring reliable electrical connections.
4. Shunt Resistor Fabrication
a. Cutting and Shaping
Shunt resistors are cut and shaped from larger blocks of conductive material, ensuring precise dimensions for accurate current measurement.
b. Soldering and Assembly
The final assembly involves soldering the shunt resistors onto circuit boards or connecting them to other components.
D. Testing and Quality Assurance
1. Electrical Testing
Each resistor undergoes rigorous electrical testing to verify its resistance value, tolerance, and performance under load conditions.
2. Environmental Testing
Environmental testing ensures that the resistors can withstand various conditions, such as temperature fluctuations and humidity.
3. Reliability Testing
Reliability testing assesses the long-term performance of the resistors, ensuring they meet industry standards and customer expectations.
V. Innovations in Current Sensing Resistor Manufacturing
A. Advances in Materials Science
1. Nanomaterials
The incorporation of nanomaterials in resistor manufacturing has led to improved performance characteristics, such as enhanced sensitivity and reduced size.
2. Composite Materials
Composite materials are being explored to create resistors with tailored properties, combining the benefits of different materials for optimal performance.
B. Automation and Industry 4.0
1. Smart Manufacturing Techniques
Automation in manufacturing processes has increased efficiency and precision, allowing for higher production rates and reduced costs.
2. Data Analytics in Production
Data analytics is being utilized to monitor production processes in real-time, enabling quick adjustments and improving overall quality.
C. Environmental Considerations
1. Sustainable Manufacturing Practices
Manufacturers are increasingly adopting sustainable practices, such as reducing waste and energy consumption, to minimize their environmental impact.
2. Recycling and Waste Management
Efforts are being made to recycle materials used in resistor production and manage waste effectively, contributing to a circular economy.
VI. Challenges in Manufacturing Current Sensing Resistors
A. Cost Management
Managing production costs while maintaining quality is a significant challenge for manufacturers, especially with fluctuating raw material prices.
B. Supply Chain Issues
Global supply chain disruptions can impact the availability of raw materials, leading to delays in production and increased costs.
C. Meeting Industry Standards and Regulations
Manufacturers must navigate complex industry standards and regulations, ensuring their products comply with safety and performance requirements.
VII. Future Trends in Current Sensing Resistor Manufacturing
A. Miniaturization and Integration
As electronic devices become smaller and more integrated, the demand for miniaturized current sensing resistors will continue to rise, driving innovation in manufacturing techniques.
B. Enhanced Performance Metrics
Future resistors will likely feature enhanced performance metrics, such as improved accuracy, lower power consumption, and greater thermal stability.
C. Emerging Applications in Electric Vehicles and Renewable Energy
The growing adoption of electric vehicles and renewable energy systems presents new opportunities for current sensing resistors, necessitating advancements in their design and manufacturing.
VIII. Conclusion
A. Summary of Key Points
Current sensing resistors are essential components in modern electronics, with various types and manufacturing processes that cater to diverse applications. The advancements in materials science, automation, and sustainable practices are shaping the future of resistor manufacturing.
B. The Role of Current Sensing Resistors in Future Technologies
As technology continues to evolve, the role of current sensing resistors will become increasingly critical in ensuring the efficiency and safety of electronic systems.
C. Final Thoughts on Manufacturing Innovations
The ongoing innovations in the manufacturing processes of current sensing resistors will not only enhance their performance but also contribute to the development of smarter, more sustainable electronic devices. As we look to the future, the importance of these components in driving technological advancements cannot be overstated.