Common Production Processes for Parallel Capacitors
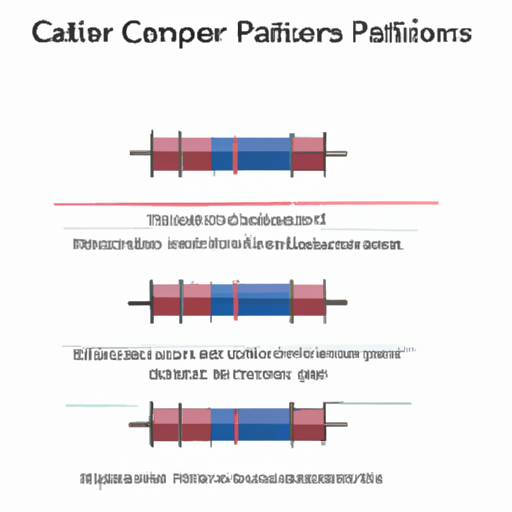
I. Introduction
A. Definition of Parallel Capacitors
Parallel capacitors are capacitors connected in such a way that they share the same voltage across their terminals. This configuration allows for an increase in the total capacitance, which is the sum of the individual capacitances. Parallel capacitors are widely used in electronic circuits to enhance performance, stabilize voltage, and filter signals.
B. Importance of Capacitors in Electronic Circuits
Capacitors play a crucial role in electronic circuits, serving various functions such as energy storage, voltage smoothing, and signal coupling. They are essential components in power supply circuits, audio equipment, and communication devices. The ability to combine multiple capacitors in parallel allows designers to achieve desired capacitance values while optimizing size and performance.
C. Overview of the Production Process
The production of parallel capacitors involves several key processes, from material selection to final testing. Understanding these processes is vital for manufacturers aiming to produce high-quality capacitors that meet industry standards.
II. Types of Parallel Capacitors
A. Ceramic Capacitors
Ceramic capacitors are made from ceramic materials and are known for their stability and reliability. They are commonly used in high-frequency applications due to their low equivalent series resistance (ESR).
B. Electrolytic Capacitors
Electrolytic capacitors are polarized capacitors that offer high capacitance values in a relatively small package. They are often used in power supply circuits but require careful handling due to their polarity.
C. Film Capacitors
Film capacitors use a thin plastic film as the dielectric material. They are known for their excellent stability and low loss characteristics, making them suitable for audio and high-frequency applications.
D. Tantalum Capacitors
Tantalum capacitors are known for their high capacitance-to-volume ratio and reliability. They are often used in applications where space is limited, such as in mobile devices.
E. Comparison of Different Types
Each type of capacitor has its advantages and disadvantages, making them suitable for different applications. For instance, ceramic capacitors are ideal for high-frequency applications, while electrolytic capacitors are preferred for power supply circuits due to their high capacitance.
III. Raw Materials Used in Capacitor Production
A. Dielectric Materials
1. Types of Dielectrics
The dielectric material is crucial for capacitor performance. Common dielectrics include ceramic, polyester, polypropylene, and tantalum oxide. Each material has unique properties that affect the capacitor's performance.
2. Properties Required for Dielectrics
Dielectric materials must possess high insulation resistance, low dielectric loss, and stability over a range of temperatures and frequencies. These properties ensure that the capacitor operates efficiently and reliably.
B. Conductive Materials
1. Metals Used (e.g., Aluminum, Tantalum)
Conductive materials are essential for the electrodes of capacitors. Aluminum and tantalum are commonly used due to their excellent conductivity and corrosion resistance.
2. Conductive Coatings
In some capacitor designs, conductive coatings are applied to enhance conductivity and improve performance. These coatings can be made from various materials, including silver and copper.
C. Packaging Materials
1. Types of Packaging
Packaging materials protect capacitors from environmental factors and mechanical stress. Common packaging types include plastic, metal cans, and ceramic enclosures.
2. Importance of Packaging in Performance
The choice of packaging material can significantly impact the capacitor's performance, especially in terms of thermal management and moisture resistance.
IV. Common Production Processes
A. Material Preparation
1. Sourcing and Quality Control
The production process begins with sourcing high-quality raw materials. Manufacturers must implement strict quality control measures to ensure that the materials meet industry standards.
2. Material Processing Techniques
Once sourced, materials undergo various processing techniques, such as grinding, mixing, and drying, to prepare them for capacitor production.
B. Dielectric Layer Formation
1. Methods of Dielectric Layer Creation
The dielectric layer is a critical component of capacitors. Several methods are used to create this layer, including:
a. Coating
In this method, a dielectric material is applied as a thin layer over a substrate.
b. Deposition
Deposition techniques, such as chemical vapor deposition (CVD) and physical vapor deposition (PVD), are used to create uniform dielectric layers.
c. Laminating
Laminating involves stacking multiple layers of dielectric materials to achieve the desired thickness and properties.
C. Electrode Fabrication
1. Techniques for Electrode Production
Electrode fabrication is another crucial step in capacitor production. Common techniques include:
a. Stamping
Stamping is used to cut electrodes from metal sheets, ensuring precise dimensions.
b. Etching
Etching involves removing material from the surface of the electrode to create specific patterns and features.
c. Sputtering
Sputtering is a deposition technique that allows for the creation of thin films of conductive materials on the dielectric layer.
D. Assembly of Capacitor Components
1. Layer Stacking
After the dielectric and electrodes are prepared, they are stacked in layers to form the capacitor structure. This process requires precision to ensure proper alignment and contact.
2. Connection of Electrodes
The electrodes are then connected to external leads, allowing the capacitor to be integrated into electronic circuits.
E. Encapsulation and Packaging
1. Types of Encapsulation
Encapsulation protects the capacitor from environmental factors. Common methods include potting, encapsulation in resin, and using heat-shrink tubing.
2. Importance of Environmental Protection
Proper encapsulation is essential for ensuring the longevity and reliability of capacitors, especially in harsh environments.
V. Quality Control and Testing
A. Importance of Quality Control in Capacitor Production
Quality control is critical in capacitor production to ensure that the final products meet performance and safety standards. Manufacturers must implement rigorous testing protocols throughout the production process.
B. Testing Methods
1. Electrical Testing
Electrical testing measures parameters such as capacitance, ESR, and leakage current to ensure that the capacitors perform as expected.
2. Mechanical Testing
Mechanical testing assesses the physical integrity of capacitors, including their resistance to vibration and shock.
3. Environmental Testing
Environmental testing evaluates how capacitors perform under various conditions, such as temperature extremes and humidity.
C. Standards and Certifications
Manufacturers must adhere to industry standards and obtain certifications to ensure that their capacitors are safe and reliable. Common standards include ISO, IEC, and RoHS compliance.
VI. Innovations in Capacitor Production
A. Advances in Materials Science
Recent advancements in materials science have led to the development of new dielectric and conductive materials, improving capacitor performance and reliability.
B. Automation and Robotics in Manufacturing
The integration of automation and robotics in capacitor production has increased efficiency and precision, reducing production costs and improving quality.
C. Sustainable Practices in Production
Sustainability is becoming increasingly important in capacitor production. Manufacturers are exploring eco-friendly materials and processes to minimize their environmental impact.
VII. Conclusion
A. Summary of Key Points
The production of parallel capacitors involves a complex series of processes, from material selection to final testing. Understanding these processes is essential for manufacturers aiming to produce high-quality capacitors.
B. Future Trends in Capacitor Production
As technology continues to evolve, the demand for more efficient and reliable capacitors will grow. Innovations in materials, automation, and sustainability will shape the future of capacitor production.
C. The Role of Parallel Capacitors in Modern Electronics
Parallel capacitors are integral to modern electronic devices, enabling improved performance and functionality. As electronic circuits become more complex, the importance of high-quality capacitors will only increase.
VIII. References
A. Academic Journals
- Journal of Applied Physics
- IEEE Transactions on Electron Devices
B. Industry Reports
- Capacitor Market Analysis Report
- Trends in Capacitor Technology
C. Manufacturer Guidelines
- Capacitor Manufacturing Best Practices
- Quality Control Standards for Capacitors
This blog post provides a comprehensive overview of the common production processes for parallel capacitors, highlighting the importance of each step in ensuring high-quality electronic components.
Common Production Processes for Parallel Capacitors
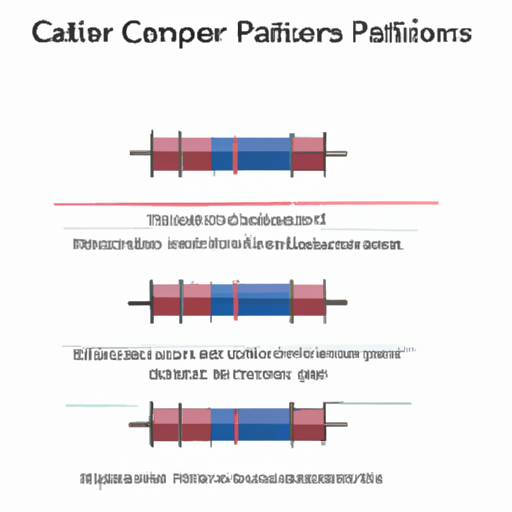
I. Introduction
A. Definition of Parallel Capacitors
Parallel capacitors are capacitors connected in such a way that they share the same voltage across their terminals. This configuration allows for an increase in the total capacitance, which is the sum of the individual capacitances. Parallel capacitors are widely used in electronic circuits to enhance performance, stabilize voltage, and filter signals.
B. Importance of Capacitors in Electronic Circuits
Capacitors play a crucial role in electronic circuits, serving various functions such as energy storage, voltage smoothing, and signal coupling. They are essential components in power supply circuits, audio equipment, and communication devices. The ability to combine multiple capacitors in parallel allows designers to achieve desired capacitance values while optimizing size and performance.
C. Overview of the Production Process
The production of parallel capacitors involves several key processes, from material selection to final testing. Understanding these processes is vital for manufacturers aiming to produce high-quality capacitors that meet industry standards.
II. Types of Parallel Capacitors
A. Ceramic Capacitors
Ceramic capacitors are made from ceramic materials and are known for their stability and reliability. They are commonly used in high-frequency applications due to their low equivalent series resistance (ESR).
B. Electrolytic Capacitors
Electrolytic capacitors are polarized capacitors that offer high capacitance values in a relatively small package. They are often used in power supply circuits but require careful handling due to their polarity.
C. Film Capacitors
Film capacitors use a thin plastic film as the dielectric material. They are known for their excellent stability and low loss characteristics, making them suitable for audio and high-frequency applications.
D. Tantalum Capacitors
Tantalum capacitors are known for their high capacitance-to-volume ratio and reliability. They are often used in applications where space is limited, such as in mobile devices.
E. Comparison of Different Types
Each type of capacitor has its advantages and disadvantages, making them suitable for different applications. For instance, ceramic capacitors are ideal for high-frequency applications, while electrolytic capacitors are preferred for power supply circuits due to their high capacitance.
III. Raw Materials Used in Capacitor Production
A. Dielectric Materials
1. Types of Dielectrics
The dielectric material is crucial for capacitor performance. Common dielectrics include ceramic, polyester, polypropylene, and tantalum oxide. Each material has unique properties that affect the capacitor's performance.
2. Properties Required for Dielectrics
Dielectric materials must possess high insulation resistance, low dielectric loss, and stability over a range of temperatures and frequencies. These properties ensure that the capacitor operates efficiently and reliably.
B. Conductive Materials
1. Metals Used (e.g., Aluminum, Tantalum)
Conductive materials are essential for the electrodes of capacitors. Aluminum and tantalum are commonly used due to their excellent conductivity and corrosion resistance.
2. Conductive Coatings
In some capacitor designs, conductive coatings are applied to enhance conductivity and improve performance. These coatings can be made from various materials, including silver and copper.
C. Packaging Materials
1. Types of Packaging
Packaging materials protect capacitors from environmental factors and mechanical stress. Common packaging types include plastic, metal cans, and ceramic enclosures.
2. Importance of Packaging in Performance
The choice of packaging material can significantly impact the capacitor's performance, especially in terms of thermal management and moisture resistance.
IV. Common Production Processes
A. Material Preparation
1. Sourcing and Quality Control
The production process begins with sourcing high-quality raw materials. Manufacturers must implement strict quality control measures to ensure that the materials meet industry standards.
2. Material Processing Techniques
Once sourced, materials undergo various processing techniques, such as grinding, mixing, and drying, to prepare them for capacitor production.
B. Dielectric Layer Formation
1. Methods of Dielectric Layer Creation
The dielectric layer is a critical component of capacitors. Several methods are used to create this layer, including:
a. Coating
In this method, a dielectric material is applied as a thin layer over a substrate.
b. Deposition
Deposition techniques, such as chemical vapor deposition (CVD) and physical vapor deposition (PVD), are used to create uniform dielectric layers.
c. Laminating
Laminating involves stacking multiple layers of dielectric materials to achieve the desired thickness and properties.
C. Electrode Fabrication
1. Techniques for Electrode Production
Electrode fabrication is another crucial step in capacitor production. Common techniques include:
a. Stamping
Stamping is used to cut electrodes from metal sheets, ensuring precise dimensions.
b. Etching
Etching involves removing material from the surface of the electrode to create specific patterns and features.
c. Sputtering
Sputtering is a deposition technique that allows for the creation of thin films of conductive materials on the dielectric layer.
D. Assembly of Capacitor Components
1. Layer Stacking
After the dielectric and electrodes are prepared, they are stacked in layers to form the capacitor structure. This process requires precision to ensure proper alignment and contact.
2. Connection of Electrodes
The electrodes are then connected to external leads, allowing the capacitor to be integrated into electronic circuits.
E. Encapsulation and Packaging
1. Types of Encapsulation
Encapsulation protects the capacitor from environmental factors. Common methods include potting, encapsulation in resin, and using heat-shrink tubing.
2. Importance of Environmental Protection
Proper encapsulation is essential for ensuring the longevity and reliability of capacitors, especially in harsh environments.
V. Quality Control and Testing
A. Importance of Quality Control in Capacitor Production
Quality control is critical in capacitor production to ensure that the final products meet performance and safety standards. Manufacturers must implement rigorous testing protocols throughout the production process.
B. Testing Methods
1. Electrical Testing
Electrical testing measures parameters such as capacitance, ESR, and leakage current to ensure that the capacitors perform as expected.
2. Mechanical Testing
Mechanical testing assesses the physical integrity of capacitors, including their resistance to vibration and shock.
3. Environmental Testing
Environmental testing evaluates how capacitors perform under various conditions, such as temperature extremes and humidity.
C. Standards and Certifications
Manufacturers must adhere to industry standards and obtain certifications to ensure that their capacitors are safe and reliable. Common standards include ISO, IEC, and RoHS compliance.
VI. Innovations in Capacitor Production
A. Advances in Materials Science
Recent advancements in materials science have led to the development of new dielectric and conductive materials, improving capacitor performance and reliability.
B. Automation and Robotics in Manufacturing
The integration of automation and robotics in capacitor production has increased efficiency and precision, reducing production costs and improving quality.
C. Sustainable Practices in Production
Sustainability is becoming increasingly important in capacitor production. Manufacturers are exploring eco-friendly materials and processes to minimize their environmental impact.
VII. Conclusion
A. Summary of Key Points
The production of parallel capacitors involves a complex series of processes, from material selection to final testing. Understanding these processes is essential for manufacturers aiming to produce high-quality capacitors.
B. Future Trends in Capacitor Production
As technology continues to evolve, the demand for more efficient and reliable capacitors will grow. Innovations in materials, automation, and sustainability will shape the future of capacitor production.
C. The Role of Parallel Capacitors in Modern Electronics
Parallel capacitors are integral to modern electronic devices, enabling improved performance and functionality. As electronic circuits become more complex, the importance of high-quality capacitors will only increase.
VIII. References
A. Academic Journals
- Journal of Applied Physics
- IEEE Transactions on Electron Devices
B. Industry Reports
- Capacitor Market Analysis Report
- Trends in Capacitor Technology
C. Manufacturer Guidelines
- Capacitor Manufacturing Best Practices
- Quality Control Standards for Capacitors
This blog post provides a comprehensive overview of the common production processes for parallel capacitors, highlighting the importance of each step in ensuring high-quality electronic components.